
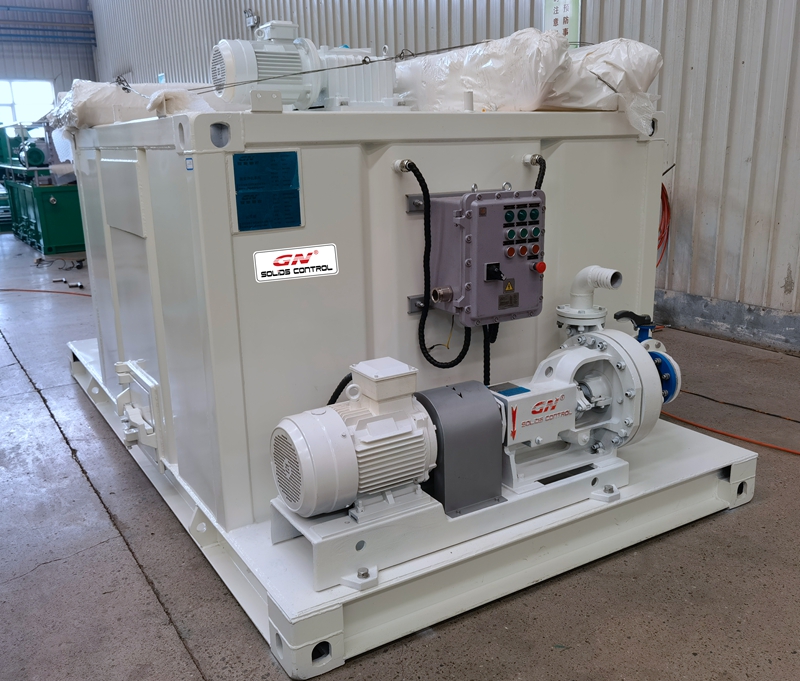
Properly ground and refined bentonite is added to fresh water to produce a “mud.” The mud reduces drilling torque, and gives stability and support to the bored hole.įluid mixing is done accurately based on specific proportions because the drilling fluid must have sufficient gel strength to keep cuttings suspended for transport, and to provide lubrication between the pipe and the borehole on pullback.ĭrilling fluids are designed to match the soil and cutter. The primary clay for drilling mud / drilling fluid is sodium montmorillonite (bentonite).

If clay represents a large component of the native soil in the construction site, a polymer additive may be more appropriate. Drilling mud can be made from clay or polymers. Hence different Types of drilling fluids are manufactured. This is the main function of drilling fluid.ĭrilling fluid properties depend on different factors, one of them is the soil components. Usually a “drilling mud” such as fluid bentonite clay is injected into the bore during cutting and reaming to stabilize the bore hole and remove soil cuttings.

What is Drilling Fluid and why do you need to add drilling fluids during horizontal drilling?
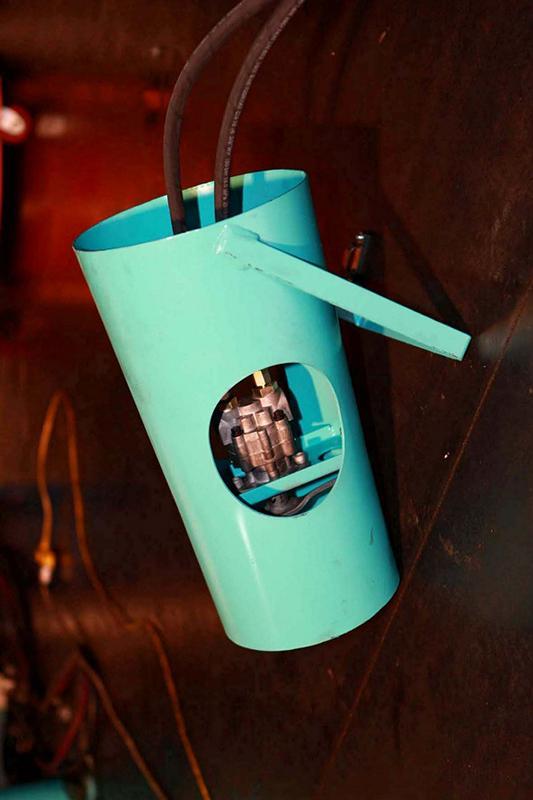
Drain your MX300 with two drainage points, activated with the opening of two easily accessible valves. Serviceability is efficient, with convenient access to the roll jets through the top of the tank. The narrow rectangular tank design can help maximize fluid volume and can be mounted for convenient transport and storage. A single or dual tank can be paired with just one power unit, allowing for the option of more drilling fluid onsite. With the option to arrange your setup to meet the jobsite needs, this mix system can be configured through mounting the tank in a variety of positions related to the power unit. The right size mixing system is key for drilling operations, and the MX300 mixing system can help you achieve maximum productivity.
